世界最高レベルの封じ込め技術を有する製造棟「FJ2」に続き、持続可能な地球環境の実現に貢献するバイオ原薬製造棟「UK4」を稼働させた中外製薬。それは前例のない、チャレンジングな建設プロジェクトだった。プロジェクトに携わった3人が、同社の製薬・生産技術の強み、次世代の製造基盤の確立に向けた想いを語る。(インタビュイー:天沼、後藤、平澤)
※中外製薬公式talentbook(https://www.talent-book.jp/chugai-pharm)より転載。記載内容・所属は2024年11月時点のものです
CPMCの高い製薬・生産機能で、新薬を一秒でも早く世界中の患者さんに届けたい
中外製薬グループの中で、中外製薬工業(以下、CPMC)が担うのは開発と生産機能。治験薬や製品の製法プロセスを中外製薬から受け取り、工場での生産体制を構築し、生産と品質管理までを手がけている。世界的に高く評価される中外製薬の創薬力。それを支えるのが、CPMCの製薬・生産技術だ。CPMCの強みとめざす姿を3人はこう語る。
平澤:医薬品には低分子、中分子、抗体といった多様な創薬モダリティ(創薬技術の分類)があります。CPMCは東京都北区の浮間工場、栃木県宇都宮市の宇都宮工場、静岡県藤枝市の藤枝工場の3つの製造拠点があり、低分子と中分子医薬品の製造は藤枝工場、抗体医薬品は浮間と宇都宮工場で製造しています。
各拠点でそれぞれのモダリティの製造技術に精通したメンバーが、「患者中心」の価値観のもと、一人ひとりの知見や経験を最大限に活かし、難易度の高いモダリティの製造技術を確立していることが、私たちの大きな強みです。
とくに、中外製薬の医薬品は、少量で人体に強い薬効を与える「高薬理活性」といわれる物質が多いため、これらを従業員が安全に取り扱える施設が必要なのですが、高い封じ込め技術によって高薬理活性原薬と製剤の製造を可能にしています。研究と臨床開発活動の進捗に応じた柔軟かつ最適な製造基盤を持っていることも、CPMCの競争力になると考えています。
後藤:中外製薬は、バイオ医薬や独自の抗体エンジニアリング技術が世界的に評価されています。その生産技術においても、複雑な構造を持つ抗体の工業化を実現しています。さらに、製造プロセスを止めずに稼働し続ける「連続生産機能」の実装により生産効率化、コストダウンや環境負荷の低減をめざした製造工程の構築に取り組んでいます。
中外製薬が戦略的アライアンスを組むロシュ社と共同で戦略プロジェクトを推進していることもCPMCの大きな特徴です。新たな技術の妥当性や、規制要件やガイドラインに対する解釈の適切性などを、ロシュ・グループのエンジニアと議論を重ねながら、設備の設計に反映させています。
天沼:CPMCは2030年の将来像として、「最速の開発スピードと信頼の品質を実現し、革新的医薬品を待っている世界の人々から必要とされる、生産機能のトップランナー」を掲げています。
このビジョン達成に向けて、5つの変革への目標「ポーラスター」を設定しました。開発スピード倍増、製造期間の短縮、正確で信頼できる品質の追求、安定供給による医薬品の付加価値倍増、そして人財育成を通じた医薬品製造の強化を指標に、社員一人ひとりが意識して行動しています。
中外製薬では2019年以降、生産・製薬技術の強化に向けた設備投資を加速。この取り組みの一環として複数の最先端製造施設の建設が進められる中、平澤は藤枝工場のFJ2、後藤と天沼は浮間工場のUK4の建設プロジェクトに携わってきた。
平澤:FJ2の建設プロジェクトに設備設計担当のプロジェクトマネジャーとして参画しました。SME(Subject Matter Expert:その分野の専門家)という立場で、一部の設備設計も担当しています。
後藤:私はUK4の建設プロジェクトリーダーを担当しました。各チームのリーダーと緊密に連携しながら、プロジェクト全体を統括し、円滑に進行させることが役割です。
天沼:UK4の建設プロジェクトにおいて私が務めたのは、ユーザーチームのリーダーのポジションです。開発、製造、品質管理など、さまざまな部門のニーズを的確に把握し、それらを設計に反映させることで、製造効率が高くユーザーフレンドリーな設備の実現をめざしました。
協業の力で乗り越えた壁。世界最高レベルの封じ込め技術実現までの道のり
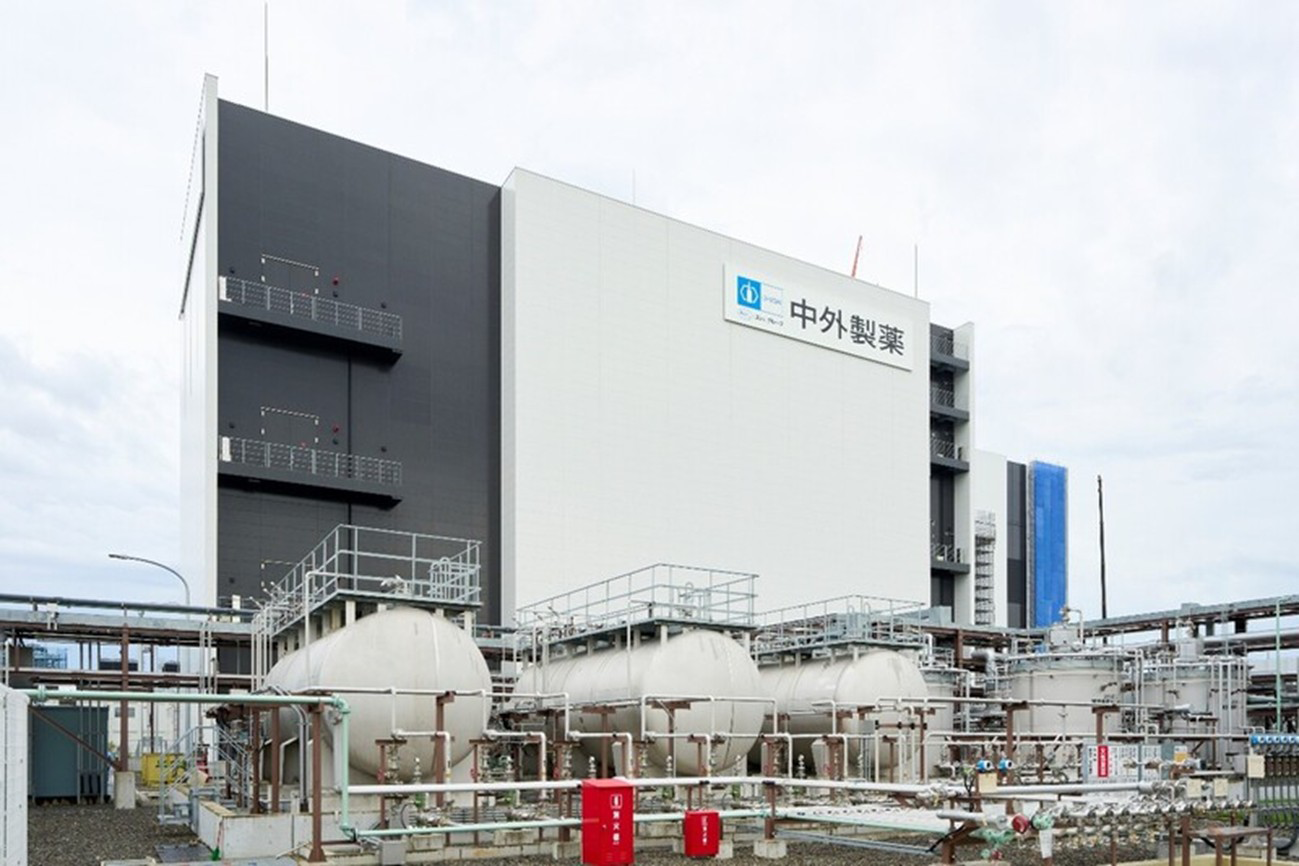
2022年12月に稼働したFJ2は、低分子と中分子の早期開発用の治験薬製造を担う。異なるモダリティを同じ建屋で製造することに加え、中分子医薬は、高薬理活性、かつ溶けにくい難溶解性のため、前例のない製造設備が求められた。プロジェクトを振り返って平澤はこう語る。
平澤:FJ2プロジェクトが始動したのは2015年ごろ。研究開発から商用生産までのスピーディーな供給体制を構築することが目的でした。
FJ2のコンセプトは、低・中分子医薬品の両方を製造できる設備の実現です。まず、低分子と中分子とでは製造プロセスが異なるため、非常にチャレンジングな取り組みでした。製造プロセスが異なるということは、それぞれの製造で使用する設備が大きく異なります。製造設備の大きさは大小さまざまで、限られたスペースに両方の製造プロセスの要求を満たす設備を如何にして配置するか、パズルのような検討を繰り返し実施しました。
さらに、高い薬理活性の中分子医薬品を取り扱うにあたって、製造作業を行う社員の安全確保するため、気中濃度0.05㎍/㎥以下という極めて気密度の高い封じ込めを達成しています。イメージしにくいかもしれませんが、これは、東京ドーム20個分の容積の中で、角砂糖1個分の漏洩も許されない厳密さです。
高い封じ込め技術だけでなく、FJ2では地球環境への配慮から、中外製薬で初めて自然冷熱媒の導入と、製品切り替え時の洗浄期間を約3分の1に短縮し、洗浄しやすい設備設計を採用し環境負荷の低減を図っています。洗浄期間を短縮することにより、洗浄で用いる原材料が不要となり、結果として余計な廃棄物が発生せず廃棄量の減少につながります。
さらに、製造設備では製品以外の物質を混入させないため、前の製造工程が完了しない限り次の工程を開始できないため、洗浄期間の短縮は新薬の開発に向けた生産効率の向上につながります。
プロジェクトに取り組むに当たり、平澤たちはロシュとも密にコミュニケーションを取り、彼らの知見も最大限に生かした。
平澤:ロシュとのディスカッション通じて、コンセプトの解像度を高めていきました。スイス・バーゼルの本社を訪問し、設計内容の妥当性を検討し、それに基づき精緻化を図る議論を行いました。
日本にはまだない製造設備を見学させてもらい、当社の設備に取り入れることはできないかと、ロシュのエンジニアが一緒になって考えてくれる。彼らのアドバイスや知見を活かすことができるのは、当社ならではのプロセスで、協業のメリットを強く感じました。
世界最高水準の封じ込め技術実現の鍵となったのは、協力会社であるエンジニアリング企業との協業だった。
平澤:最大の課題は、協力会社にコンセプトを理解してもらい、同じゴールをめざすことでした。当初、われわれのコンセプトに対し、協力会社からは実現は困難だろうと懸念を抱かれていたからです。この状況を打破するため、具体的なデータを示しながら目標達成の可能性を説明し、彼らの不安を1つずつ解消していきました。
建設プロジェクトは、設備の品質のみならず達成すべきコスト、スケジュールが厳格に定められています。品質を満たすためにコスト、スケジュールを変更することは許されず、これらのバランスを維持しながら進めることが大切です。
封じ込めを達成するという高い要求に応えるために、技術的な点だけではなく、われわれが望むコスト、スケジュールを満たすように試行錯誤し、アイデアをひねり出してくれました。前例のないチャレンジに向かって同じ方向を向き、ともに粘り強く戦い続けたことで、品質、コスト、スケジュールの要件を満たすことができたと、実感しています。
立場の異なる企業同士が同じ方向を向くことは容易ではありません。このプロジェクトが成功したのは、革新的な技術開発があったからではなく、知識を持つ多くの関係者を巻き込み、粘り強くPDCAサイクルを回し続けたからだと考えています。
このプロジェクトを通じて、高度な技術開発においては、技術面だけでなく関係者との信頼関係が極めて重要であることを学びました。互いに価値ある結果となり、Win-Winの関係を築けたことを非常に喜ばしく思っています。
中外製薬が挑む次世代バイオ製造施設。3ゼロ実現と臨床開発の迅速化に向けて
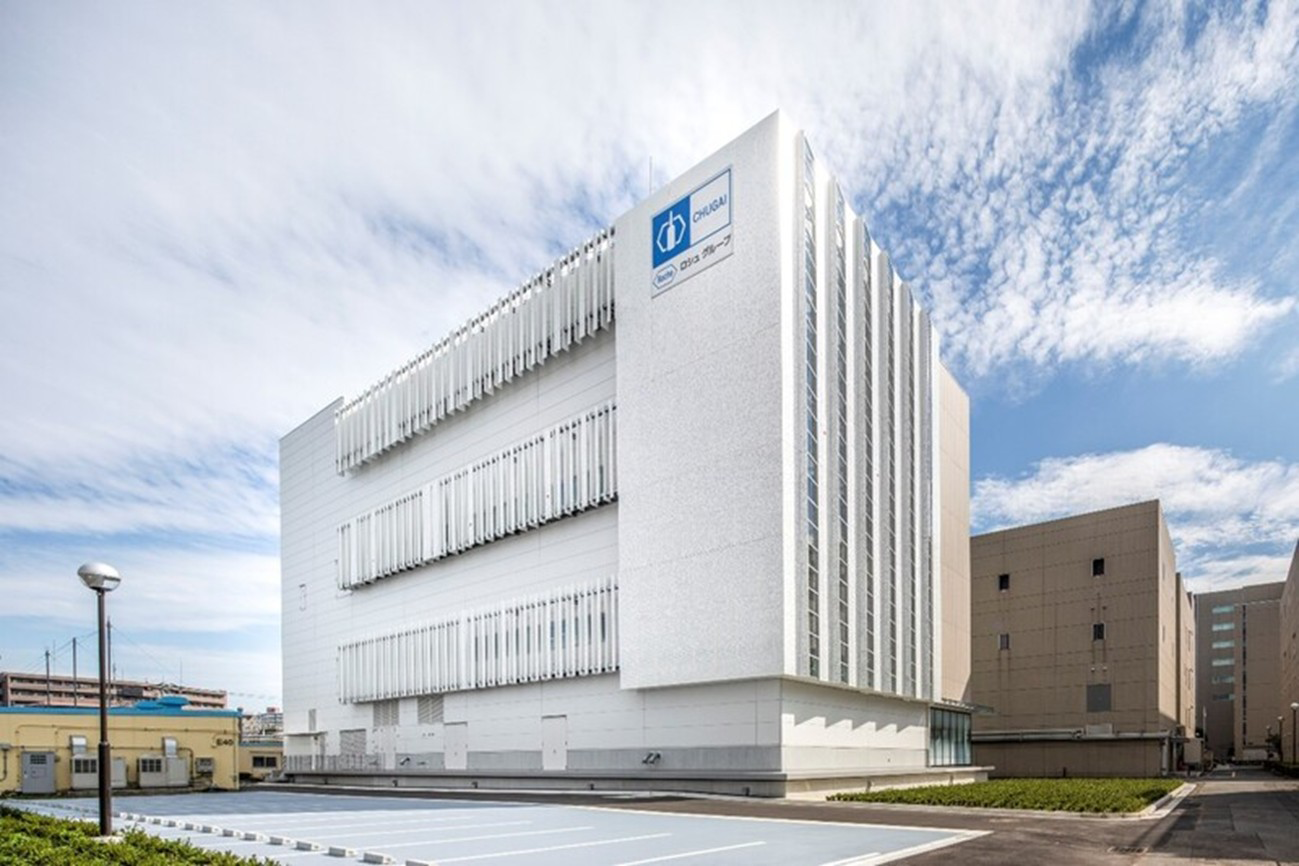
UK4は2024年1月に稼働した。UK4の建設により、初期臨床開発から初期商用生産までの一貫した自社供給力が強化された。加えて、環境負荷低減にも貢献している。
後藤:第一に、これまで中外製薬には治験薬専用の製造ラインがなかったため、新規医薬品の速やかな開発・上市を支える製造基盤を強化する狙いがありました。UK4は製品ごとに製造方法を柔軟に変更できる設計としました。また、自社製造により、研究開発の進捗や臨床試験計画に応じた迅速な治験薬製造が可能となりました。
第二に、中外製薬では2021年に「中長期環境目標2030」を策定しています。持続可能な地球環境の実現に貢献するため、環境負荷の低減と省エネルギーの設計に取り組みました。「持続可能な社会に向けた3ゼロ」をコンセプトに「フロンゼロ・ガスゼロ・CO₂ゼロ」の実現をめざしています。
冷熱源には自然冷媒機器を採用し、ガスボイラーから電気ボイラーへの転換を図り、太陽光パネルを設置すると同時に、浮間地区全体で自然エネルギー由来のサステナブル電力を活用することで、総合的なCO₂排出ゼロを達成しました。
天沼:さらに、UK4の新たな取り組みとして、従来はステンレス製が主流だった製造設備を、使い捨てであるシングルユースの設備に転換しました。ステンレス製設備では、医薬品の製造後に設備を洗浄・滅菌する必要があり、多くの時間を費やします。それだけでなく、洗浄・滅菌のためには大量の水と蒸気を消費し、それらを作るために多くのエネルギーを使用します。
シングルユース設備の利活用によって、設備の柔軟性を高めることで、製法プロセスの変更に対応することができますし、エネルギー使用量の削減だけでなく、次の製造への移行期間の短縮が期待されています。
しかし、UK4の建設プロジェクトが始まったのはコロナ禍の真っ只中。物資や人員の調達など、想定通りにいかず、これまでにない課題に直面したと言う。
後藤:全世界で新型コロナウイルス感染症の治験薬やワクチン開発が急務となり、国内外で、製造プラント建設増による建築資材の不足、シングルユース設備の受注過多、原材料不足の状況となりました。加えて半導体の需要増に伴う電子部品不足の影響も大きく、これまでの建設プロセスとは異なる状況下でのプロジェクト進行となりました。
ただ、そうした状況は予見できていたので、シングルユース設備やシングルユースバックを先行で注文し、先行で納品された設備や資材が保管できるよう、社外倉庫を確保するなど、リスクを最小化する策を講じて対応しました。
天沼:緊急事態宣言下でのプロジェクト進行となり、社内メンバーとも対面できず、コミュニケーションに苦労しました。新型コロナ用ワクチン製造の需要増でシングルユース製品の納期に遅れが生じ、調達や生産調整に苦労した他製造ラインでの経験を活かし、複数メーカーのバッグに対応できるストレージタンクを設計するなど、柔軟な対策を講じたことは、今後の生産遅延リスクの軽減にもつながると考えています。
社内外の反響を大きな手ごたえに、3人は次なるステージへ
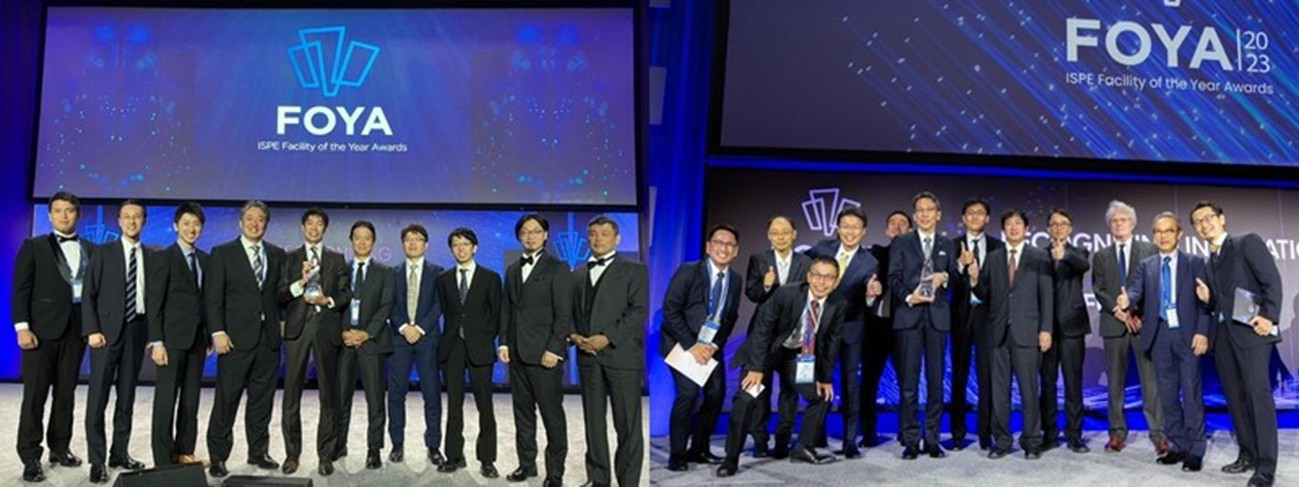
グローバルな医薬品供給チェーンにおいて、重要な役割を果たす先進的な製造設備を完成へと導いた3人。そして、FJ2とUK4は、国際製薬技術協会が実施するアワード「Facility of the Year Awards(以下、FOYA)」を受賞した。プロジェクトの成果を3人はこう振り返る。
天沼:竣工後、社内はもちろん、ロシュ・グループメンバーやメディアの見学が相次ぎました。業界内外の注目度の高さを実感し、大きな手ごたえを感じています。
現在、私はUK4におけるバイオ原薬製造管理責任者として治験薬製造の管理・運営を担当していますが、メンバーとともに高いモチベーションを持って業務に取り組む中で、このプロジェクトに参加できた喜びをあらためて噛み締めています。
平澤:FOYA賞に応募しようと考えたのは、FJ2の客観的な評価を知りたいと思ったからです。FOYA賞へのエントリー自体、CPMCにとって初めての試みだったため、社内の理解を得るのに苦労しましたが、最終的には関係者全員が一丸となって取り組んでくれました。
そして、FJ2はInnovation部門の年間優秀施設賞を受賞することができ、社内関係者だけでなく、ロシュや協力会社とも喜びを分かちあいました。2023年にラスベガスで開催された授賞式に出席しました。あのような式典に参加すること自体貴重な経験ですが、授賞式の場でのメンバーの晴れやかな笑顔や、外部の方から声を掛けられ賞賛されたことはとても感慨深いです。想像以上の反響が得られたことは、大きな自信になりました。
後藤:FJ2の受賞に続き、UK4がFOYA 2024のSocial Impact部門で年間優秀施設賞を獲得しました。日本の製薬会社の国内施設が2年連続で受賞するのは史上初の快挙で、社外関係者からもお祝いの言葉をいただきました。非常に名誉なことだと感じています。平澤さんがFJ2でFOYAに挑戦してくれたからこそ、UK4も自信をもってエントリーできました。
前例のない大きなプロジェクトでの成功を糧に、3人はさらなる高みをめざす。
平澤:今回、自分のチャレンジが道をつくり、次の人のチャレンジにつながることを実感しました。未知の領域に踏み込むことで、多くの人に刺激を与え、それが組織の発展につながればと思います。
後藤:環境と省エネの取り組みの効果について、今後はUK4の製造実績データを評価していくつもりです。その結果を対外的に積極的にアピールし、持続可能な地球環境の実現に貢献できる設備として、発信していきたいです。
天沼:これからも世界中の患者さんの期待に応えるため、UK4の設備を最大限活用し、スピードとフレキシビリティという強みを活かして高品質の治験薬を製造し、新薬の早期上市に貢献していきます。