To become a top runner in drug production. Taking on the challenge of innovative drug manufacturing with next-generation manufacturing facilities
- R&D
- Recruitment
- Sustainability
- Supply Chain Management
- Drug Discovery Modalities
- Production Technology
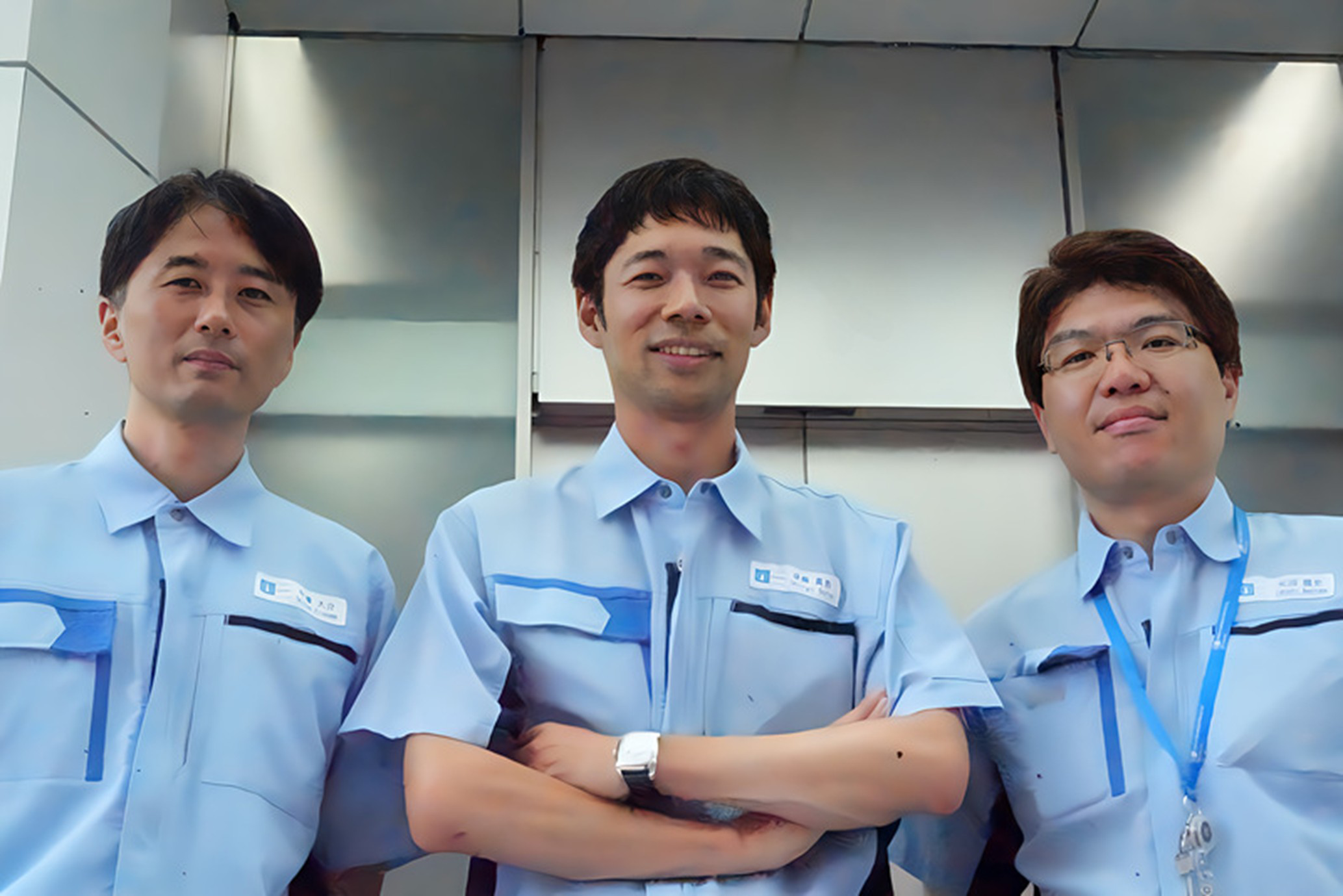
Chugai Pharmaceutical’s bio drug substance (DS) manufacturing facility “UK4,” which contributes to the realization of sustainable global environment, began operating, following on from the API manufacturing facility “FJ2,” which has world-class advanced containment technologies. These were unprecedented, highly challenging construction projects. Three members who were involved in the projects talk about the strengths of Chugai’s pharmaceutical technology and production functions and their hopes for the establishment of next-generation manufacturing bases. (Interviewees: Amanuma, Goto, and Hirasawa)
*Reproduced from Chugai Pharmaceutical’s official Talentbook website (https://www.talent-book.jp/chugai-pharm) Article details and employee positions are current as of November 2024.
We want to deliver new drugs to patients around the world as soon as possible with CPMC’s advanced drug manufacturing and production functions
Chugai Pharma Manufacturing Co. Ltd. (CPMC) is the Chugai Pharmaceutical Group company in charge of development and production functions. It has taken over the manufacturing processes for investigational and commercial products from Chugai Pharmaceutical, established production systems at its plants, and is responsible for production and quality control. Chugai Pharmaceutical’s drug discovery capabilities are held in high regard globally. Those capabilities are supported by CPMC’s pharmaceutical technology and production functions. Three members talk about CPMC’s strengths and vision.
Hirasawa: Drugs come in various therapeutic modalities (therapeutic approaches), including small and mid-size molecules and antibodies. CPMC has three manufacturing bases: Ukima Plant (Kita-ku, Tokyo), Utsunomiya Plant (Utsunomiya City, Tochigi), and Fujieda Plant (Fujieda City, Shizuoka). The Fujieda Plant manufactures small molecule and mid-size molecule drugs, while the Ukima Plant and Utsunomiya Plant manufacture therapeutic antibodies.
One of our greatest strengths is that, based on the value of patient-centricity, members with expertise in the manufacturing technologies for the respective modalities make the most of their individual knowledge and experience to establish manufacturing technologies for highly challenging modalities at each location.
In particular, as many of Chugai Pharmaceutical’s drugs are substances known as “high-potency APIs (HPAPIs)” that have a strong effect on the human body even in small amounts, facilities that will allow employees to handle these substances safely are needed. CMPC’s advanced containment technologies make it possible to manufacture HPAPIs and drug products. The flexible and appropriate way in which CPMC’s manufacturing bases are able to accommodate progress in research and clinical development activities is another competitive advantage of the company.
Goto: Chugai Pharmaceutical is recognized worldwide for its biopharmaceuticals and its unique antibody engineering technologies. In its pharmaceutical technology and production functions as well, Chugai Pharmaceutical has realized the manufacturing of antibodies with complex structures. Moreover, with the implementation of a continuous production function that allows continuous operations without suspending the manufacturing process, we are working on building manufacturing processes with the aims of more efficient production, lower costs, and reduced environmental impact.
A major distinction of CPMC is the fact that Chugai Pharmaceutical and its strategic alliance partner, Roche, are jointly working on the promotion of strategic projects. We have held many discussions with engineers from the Roche Group about the validity of new technologies and the appropriateness of our interpretations of regulatory requirements and guidelines, and the outcomes of those discussions are reflected in the design of our equipment.
Amanuma: CPMC has set forth a vision for 2030 to achieve the fastest development speeds and reliable quality and to become the top runner in production functions that is needed by people around the world who are waiting for innovative drugs.
Toward this vision, we have established “Polar Star,” our five goals for transformation. Each and every employee is working consciously toward these goals of doubling the speed of development, reducing production times, pursuing accurate and reliable quality, doubling added value of drugs through stable provision, and strengthening drug manufacture through human resources development.
Since 2019, Chugai Pharmaceutical has been accelerating its capital investment program for the strengthening of its production and manufacturing technologies. Among the several state-of-the-art manufacturing facilities under construction as a part of these efforts, Hirasawa was involved in the FJ2 construction project at the Fujieda Plant, while Goto and Amanuma were involved in the UK4 construction project at the Ukima Plant.
Hirasawa: I participated in the FJ2 construction project as the project manager in charge of equipment design. As a subject matter expert (SME), I was also responsible for designing some of the equipment.
Goto: I was a project leader on the UK4 construction project. My role was to work closely with the leaders of each team, overseeing the entire project to ensure its smooth progress.
Amanuma: My role in the UK4 construction project was as a leader of the user team. I worked to build user-friendly equipment that had high manufacturing efficiency by accurately identifying the needs of the various divisions, including development, manufacturing, and quality control, and reflecting those needs in the design.
Barriers overcome by the power of cooperation. The path toward world-class containment technologies
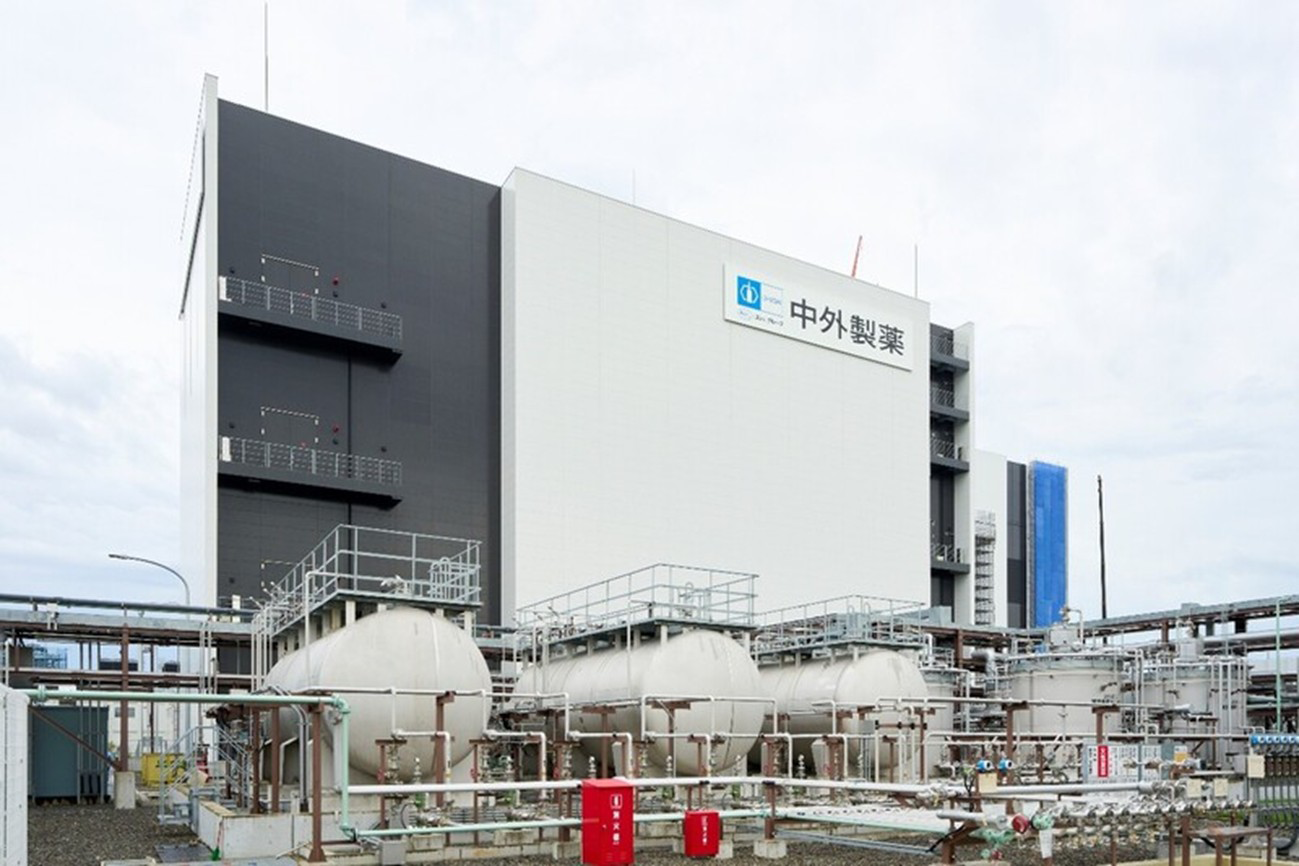
FJ2, which began operating in December 2022, is responsible for the manufacture of small and mid-size molecule investigational products for early development. Because it is planned to manufacture different modalities in the same building, and also due to the high potency and insolubility of mid-size molecule drugs, unprecedented manufacturing equipment was required. Hirasawa made the following remarks when looking back on the project.
Hirasawa: The FJ2 project was launched in around 2015. Our goal was to build a speedy supply system from R&D to commercial production.
The concept of FJ2 is to realize a facility that is able to manufacture both small and mid-size molecule drugs. As the manufacturing processes of small molecules and mid-size molecules are different, this was an extremely challenging task. Different manufacturing processes meant significant differences in the equipment used for the manufacture of each type of molecule. The manufacturing equipment came in various sizes, and we had repeated deliberations, almost like trying to complete a puzzle, about how we would arrange the equipment that met the requirements of both manufacturing processes in the limited space available.
In addition, for the handling of high-potency mid-size molecules drugs, we achieved extremely airtight containment with an air concentration of 0.05 µg/m3 or lower, to ensure the safety of employees working on their manufacture. It may be difficult to imagine, but it means that, within the volume of 20 Tokyo Domes, not even the leakage equivalent to a single cube of sugar is allowed—that is how strict the airtight containment is.
As well as advanced containment technologies, in consideration of the global environment, we are working to reduce FJ2’s environmental impact. This includes the introduction of natural cooling/heating mediums in a first for Chugai Pharmaceutical, the reduction of the cleaning period during product changeover to about one-third of its previous duration, and the adoption of equipment design that offers ease of cleaning. The reduction of the cleaning period also eliminates the need for cleaning materials, resulting in the reduction in the amount of waste generated by the plant.
In addition, to prevent the contamination of the manufacturing equipment with substances other than the product, it is not permitted to start the next process until the previous manufacturing process has been completed. For this reason, the reduction in the cleaning period helps to improve production efficiency for the development of new drugs.
While working on the project, Hirasawa and his team stayed in close communication with Roche and made the most of their knowledge.
Hirasawa: Our discussions with Roche helped us to further clarify the concept. I visited Roche’s head office in Basel, Switzerland, where we considered the appropriateness of the design details, based on which we had discussions to further refine those details.
They showed me manufacturing equipment that did not yet exist in Japan, and Roche’s engineers discussed with us how we could bring that equipment to Chugai’s facilities. This ability to make the most of their advice and knowledge is a process that is only possible at our company, and it gave me a strong sense of the benefits of the alliance.
The key to achieving world-class containment technology was cooperation with our partner engineering company.
Hirasawa: Our greatest challenge was getting our partner company to understand our concept and aim for the same goal. This is the partner company initially had concerns that our concept would be difficult to achieve. To overcome this, we used concrete data to explain to them that it would be possible to achieve our goal, dispelling their concerns one by one.
In construction projects, in addition to the quality of the equipment, the costs and schedule to be achieved are strictly defined. Changes to costs and schedule for the sake of satisfying quality are not permitted, and it is important to maintain a balance between all these factors as the project progresses.
To meet the high-level requirement of achieving containment, they worked hard to generate ideas through trial and error to meet our desired costs and schedule, alongside the technical considerations. I truly feel that we were able to meet the quality, cost, and schedule requirements as a result of our collective efforts, by facing this unprecedented challenge together, staying aligned in the same direction, and battling persistently together.
It is no easy task for companies in different positions to head in the same direction. I believe that the reason for the success of this project was not that we possessed innovative technological development, but that we drew in many relevant parties that had the knowledge required and kept implementing the PDCA cycle persistently.
Through this project, I learned that, when it comes to advanced technological development, relationships of trust with the relevant parties are just as important as the technical considerations. I am delighted that the outcome was valuable for both companies and that we were able to build a win-win relationship.
Chugai Pharmaceutical’s challenge in next-generation bio manufacturing facilities. For the realization of the three zero concept and speedier clinical development
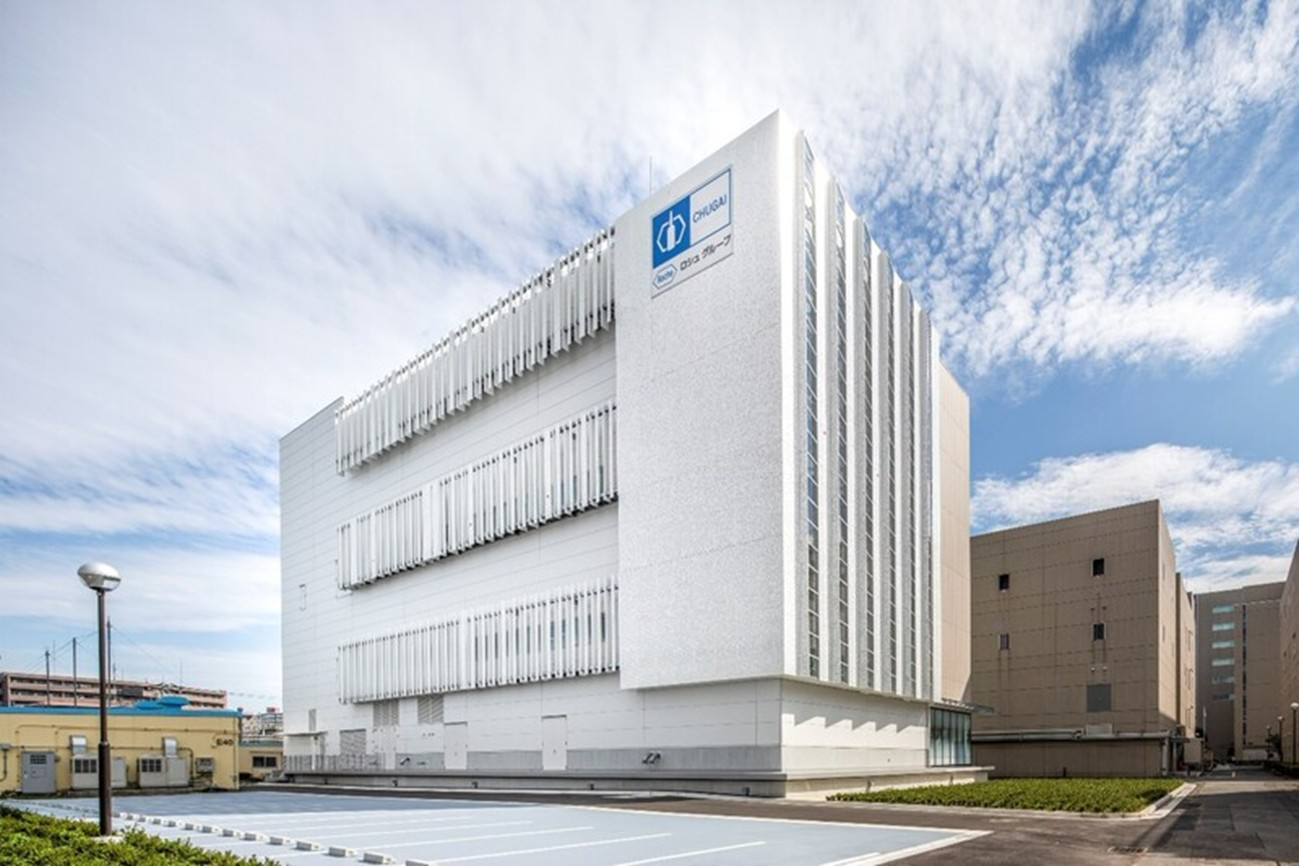
UK4 began operating in January 2024. The construction of UK4 has strengthened our integrated in-house supply capability, from early clinical development to initial commercial production. It is also contributing to the reduction of environmental impact.
Goto: Firstly, because Chugai Pharmaceutical had previously not had a dedicated manufacturing line for investigational products, one of our aims was to strengthen our manufacturing infrastructure to support the swift development and marketing of new pharmaceuticals. UK4 was designed so that the manufacturing process could be flexibly changed for each product. In addition, with in-house production, it is now possible to manufacture investigational products swiftly in accordance with progress in R&D and with clinical study plans.
Secondly, Chugai Pharmaceutical formulated its Mid- to Long-term Environmental Goals 2030 in 2021. To contribute to the realization of a sustainable global environment, we worked on the reduction of environmental impact and energy-saving design. Based on a concept of “three zeroes for a sustainable society”, we are aiming for manufacturing that is HFC-free, gas-free, and CO2-free.
In terms of cold and heat sources, we have adopted natural refrigerant equipment, we are working to transition from gas boilers to electric boilers, and we have installed solar panels. At the same time, by using sustainable electricity derived from natural energy across the entire Ukima complex, we have achieved zero CO2 emissions overall.
Amanuma: In addition, as a new initiative for UK4, we have transitioned away from stainless steel, which has been the mainstream for manufacturing equipment, to disposable single-use systems. Stainless steel systems require cleaning and sterilization after the manufacture of pharmaceuticals, which is very time-consuming. Not only that, cleaning and sterilization use large quantities of water and steam, as well as a significant amount of energy to generate them.
The use of single-use systems increases the flexibility of the equipment, and they can also accommodate changes in manufacturing processes. Not only will they reduce energy consumption, but we can also expect them to shorten the time needed when changing over to the manufacture of the next product.
However, the UK4 construction project began right in the middle of the COVID-19 pandemic. Procurement of supplies and labor did not go as well as envisaged, and the project team faced unprecedented challenges.
Goto: The development of investigational products and vaccines to combat COVID-19 worldwide became a matter of urgency. A surge in the construction of manufacturing plants led to shortages of construction materials, order overload of single-use systems, and shortages of raw materials. In addition, the shortage of electronic components caused by increased demand for semiconductors also had a major impact, and the construction project proceeded under circumstances that were different from any project that we had experienced before.
Nevertheless, because we were able to predict this situation, we ordered the single-use systems and single-use bags in advance, and we secured a warehouse outside the company to store any equipment and materials that were delivered early. In these and other ways, we responded to the situation with measures to minimize risk.
Amanuma: The project proceeded under the state of emergency declaration, which meant that we were unable to meet with in-house team members face-to-face. This made communication a challenge. With the increased demand for COVID-19 vaccine production, delays in the delivery of single-use products occurred. Leveraging the experience of other manufacturing lines that had struggled with procurement and production adjustments, we implemented flexible responses, such as designing a storage tank that could accommodate the bags of multiple manufacturers. I believe that this will help us to mitigate any future risks of production delays.
Buoyed by the strong response from both within and outside the Company, the three members are moving onto the next stage
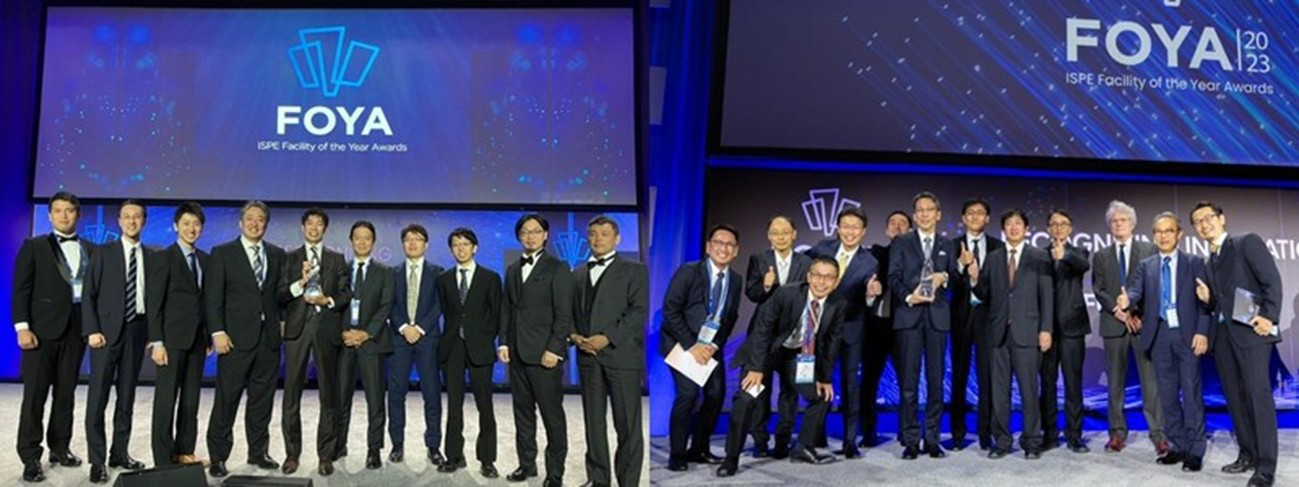
Our three interviewees helped lead the advanced manufacturing equipment, which will play a crucial role in the global pharmaceutical supply chain, to completion. FJ2 and UK4 were both recognized in the “Facility of the Year Awards” (FOYA) presented by the International Society for Pharmaceutical Engineering. The three interviewees reflected on the outcomes of the projects.
Amanuma: After the completion of construction, we welcomed successive visits from not only internal staff but also Roche Group members and the media to tour the facilities. I gained a real sense of the high level of attention that these projects attracted from both within and outside the industry, which gave me a great sense of achievement.
My current role is the management and operation of investigational product manufacture as the bio-drug substance manufacturing manager. As I engage in my work with high motivation alongside my team members, I am savoring anew the joy of having been a part of this project.
Hirasawa: We decided to enter the FOYA because we wanted to receive an objective evaluation of FJ2. The FOYA entry itself was a first for CPMC, and gaining understanding from within the company was a challenge, but ultimately, everyone involved came together and worked as one on our entry.
FJ2 was awarded a FOYA in the Innovation category, and Roche and our partner companies shared in our delight at our win alongside everyone involved at CPMC. I had the honor of attending the awards presentation ceremony in Las Vegas in 2023. Attending such a ceremony was a valuable experience in itself, but seeing the bright smiles of my team members and being praised by people outside our group was truly moving. The response we received was beyond our expectations, and it has given me a great deal of confidence.
Goto: After FJ2’s win in 2023, UK4 was named a winner in the Social Impact category in 2024. This was a historic achievement, being the first time ever for a Japanese pharmaceutical company to win two years in a row for its domestic facilities. We also received messages of congratulations from external stakeholders. I feel that it is a great honor. It was because Mr. Hirasawa embraced the challenge of entering the FOYA for FJ2 that we had the confidence to do the same for UK4.
Building on the success of these projects of unprecedented large scales, our three interviewees are now aiming for even greater heights.
Hirasawa: I have a real sense that my own challenges have opened up new paths for the people who come after me to take on challenges of their own. By stepping into unknown territory, I hope that I have inspired many other people and that this will lead to the advancement of the organization.
Goto: I intend to assess the effectiveness of our environmental and energy-saving initiatives using the UK4 manufacturing results data. I also want to actively promote those results to the outside world and present UK4 as a facility that can contribute to the realization of a sustainable global environment.
Amanuma: To continue responding to the expectations of patients all over the world, we will take maximum advantage of the UK4 facility, leveraging its strengths of speed and flexibility to manufacture high-quality investigational products and contribute to the early market launch of new drugs.